L’INDUSTRIA PESANTE DELL’ACCIAIO ‘SOSTENIBILE’: È POSSIBILE? “CERTO, HO IN MENTE UN ‘ACCIAIERIA GREEN’, E LA REALIZZEREMO NOI”. IN GRECIA
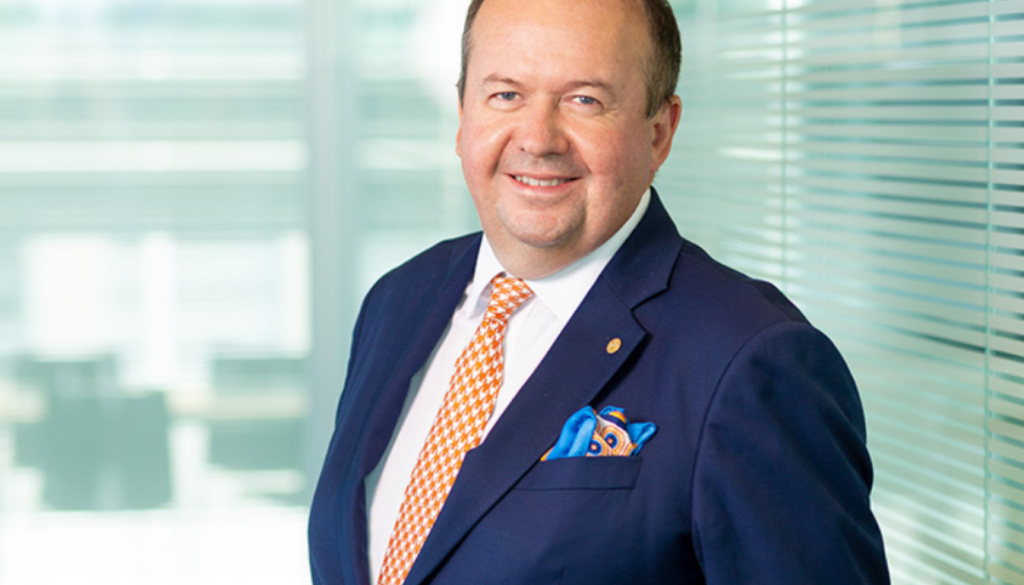
Da ciò che ho compreso, la tua è una figura professionale particolare, a metà strada tra un ingegnere fortemente specializzato e un direttore vendite. La competenza tecnica è un enorme pregio, che un venditore puro non ha, e che ti ha permesso di contribuire a far nascere intuizioni che vi hanno portato a diventare leader nella costruzione di acciaierie a basso impatto ambientale. Spiegaci innanzitutto come e dove avete innovato…
Tutto nasce da una sequenza di idee, osservando l’esistente e interrogandosi su come migliorarlo. Per fondere l’acciaio, fino al 2016 c’erano solo due sistemi, l’altoforno tradizionale e poi l’acciaio da forno elettrico, che ricicla rottami e quindi se vogliamo ha un minore impatto ambientale, ma dà qualche impurità nel prodotto finito, come quelle derivanti dalla presenza di rame, che fonde a temperature più basse, e quindi non garantisce un prodotto finale completamente omogeneo. In ogni caso, da anni non c’erano innovazioni di processo. Inoltre, con il forno elettrico è vero che si ricicla materiale preesistente, quindi apparentemente è più sostenibile, ma serve tantissima energia per fondere, 700kW per tonnellata, energia che può essere iniettata da fonte elettrica, piuttosto che da gas, etc. Immaginate però iniettare tutta questa potenza in un pentolone che può avere un diametro mediamente dai cinque a otto/nove metri, rivestito di sessanta centimetri di materiale refrattario: sono come delle ceste dentro le quali entra dentro il rottame, e che poi si aprono sul fondo, si vedono a volte anche nei film…ma lì dentro si creano continuamente cortocircuiti aperti, e questo ti obbliga ad aver reti molto performanti a livello di robustezza, perché se no “spegni” tutto quello che c’è vicino all’impianto. Inoltre, la rete lunga comporta inevitabili perdite…
Quali soluzioni avete indentificato per ovviare a questi inconvenienti?
Come primo lavoro, io progettavo anche Inverter, cioè strumenti per la conversione della corrente da alternata a continua, e poi di nuovo alternata: quando generi una conversione di questo tipo, significa che dalla corrente continua ripassi all’alternata, in poche parole sei tu che hai il controllo, e non l’elettrodo. La corrente a quel punto deve fare quello che voglio io. Quando io genero qualcosa che è controllato digitalmente, a quel punto io posso dire ai miei elettrodi, tramite un insieme di algoritmi di controllo, “voi più di questa corrente non fate passare”, qualsiasi sia il carico che hai; come un rubinetto al quale quando senti che la corrente arriva a un certo livello, tu ordini “chiuditi”, e quando ridiscende dici “riapriti”. Questo può accadere a una velocità di 500 microsecondi, cioè ogni 500 microsecondi vado a leggere quanta correte sta passando, e dico ad un microprocessore, che comunica con i transistor di potenza, di aprirsi o chiudersi come un rubinetto. Bene, diciamo che adesso abbiamo generato quello che mi serve a livello di potenza, ma non controlliamo solo la tensione, facciamo altro, un’altra cosa molto affascinante, che non puoi fare con le reti convenzionali (ad esempio la 50Hz in Europa, la 60Hz in USA, etc), cioè possiamo anche variare la frequenza, e questo ci permette di contrastare “l’effetto pelle”: con le frequenze alte, proprie della corrente alternata, essa si sposta sempre sulla superficie del conduttore, anziché transitare in tutto il conduttore come nella corrente continua; in corrente continua gli elettroni transitano in tutta la sezione del cavo, invece in corrente alternata più alzi la frequenza più essi tendono a circolare solo all’esterno della superfice (l’effetto “pelle”, appunto), e questo significa che inevitabilmente il sistema si scalda di più, e, scaldandosi il materiale, aumenta di resistenza, cioè banalizzando più si scalda più fatica fa la corrente, e più perdite ci sono… Riuscire ad abbassare la frequenza, quindi, garantisce meno “effetto pelle”, la corrente va più all’interno del conduttore, si scalda meno la superficie, e diminuiscono le perdite. Inoltre, l’arco elettrico ha una temperatura di 5500 gradi circa, quello che poi ti aiuta a fondere: più si abbassa la temperatura di frequenza, più l’arco elettrico penetra dentro l’acciaio liquido e lo scalda in minor tempo. Dal momento che parliamo in senso assoluto di consumi enormi di energia, di vere industrie energivore, ogni soluzione tecnologica finalizzata a risolvere o attutire questi problemi si rivela preziosissima. Un’acciaieria da un milione di tonnellate lavora come fondesse centomila automobili ogni mese, non so se rendo l’idea. Sia chiaro, la tecnologia Inverter esisteva già, quello che abbiamo fatto noi, con i nostri brevetti, è stato di testarla e utilizzarla, per primi al mondo, per un controllo di così alta potenza e caratterizzato da così frequenti cortocircuiti e carichi imprevisti.
Quanto le vostre soluzioni tecnologiche portano a risparmiare, rispetto ad un’acciaieria di taglia media?
Diciamo che se parliamo di forno elettrico un’acciaieria da 1 milione di tonnellate è considerata media: ce ne sono tantissime da mezzo milione, ce ne sono parecchie da un milione, e ne sono poche oltre i due milioni. Allora, anche se adesso il trend per la decarbonizzazione è quello di spostarsi verso le grandi fonderie, noi abbiamo ottenuto un sistema che ti permette di risparmiare non solo in termini di efficienza di processo ma anche di impatto ambientale. Diciamo che ad oggi possiamo migliorare l’efficienza di almeno un 10%, e se consideriamo che un’acciaieria media consuma cento milioni di dollari all’anno di energia ci rendiamo conto di cosa parliamo.
Sul fronte dell’innovazione di processo, voi siete anche riusciti a creare uno strano ma interessante “ibrido”, sotto il profilo dell’iniezione di energia che questi mega impianti necessitano per poter funzionare…
Si, il fatto di controllare il passaggio da corrente continua ad alternata e viceversa ci permette un’altra piccola “magia”: io in un modo semplice posso andare a iniettare contemporaneamente oltre all’energia che arriva dalla rete tradizionale, anche energie rinnovabili autoprodotte. Ad esempio, se nelle vicinanze del mio impianto ho un deserto (per esempio un nostro cliente sta costruendo un impianto in California, a 100 Km ad est di Los Angeles, nel deserto), ebbene, di giorno noi gli faremo funzionare l’impianto 100% con il solare, ok? Così facendo hai una flessibilità da punto dell’energy-saving, e inoltre un diverso modo di ripagarti l’investimento, perché risparmi concretamente l’energia della rete, che dovresti pagare, e dopo sei o sette anni ti sei ripagato anche l’investimento. Poi, ci avvantaggiamo anche di innovativi processi di lavorazione che ci permettono di non dover riscaldare l’acciaio per laminarlo: noi facciamo questo prodotto, i rotoli di laminato sottile, senza passare dal forno di riscaldo, ovvero dal liquido direttamente lo coliamo e lo laminiamo, senza doverlo riscaldare, e questo è un enorme vantaggio sia in termini di tempi che di impronta ecologica.
Può esistere – secondo te, oggi – un impianto per la produzione di acciaio a “zero impatto ambientale”?
Forse si, ma il problema è il costo di trasformazione. Ad esempio, se al posto del carbone metti idrogeno, l’idrogeno per produrlo devi farlo con fonti rinnovabili, e questo ha un costo, perché le devi trasformare, hai dei rendimenti, hai una resa solo del 60%…se invece immetti energia da metano, hai una certa quantità di emissioni, che sono circa il 40% di quelle di un altoforno, ma comunque ci sono. Insomma, ripeto, il sistema totalmente green e nel contempo sostenibile anche finanziariamente forse non esiste, ma quello che è certo è che possiamo ridurre l’impatto ambientale, se vogliamo, mantenendo comunque una profittabilità adeguata, questa è la mia certezza. In questo senso non ci sono più scuse. Oggi la CO2 generata dall’industria metallurgica mondiale vale l’8 per cento della CO2 generata al mondo: immagina se dovessimo, applicando queste soluzioni innovative, ridurla di venti volte. Chiaro che per essere sostenibili finanziariamente questi impianti chiedono gas a costo contenuto, e questo è un tema anche politico, anzi, geopolitico, in questo periodo di crisi con la Russia. Il tema del costo dell’energia che deve approvvigionare l’impianto – e di un eventuale ruolo dello Stato come ammortizzatore in questo senso – è enorme.
Ci sono Stati più avanti sotto questo profilo?
Un impianto 100% green lo potresti forse fare in Svezia o Norvegia. Puoi partire tranquillamente da minerale di ferro che noi chiamiamo pre-ridotto, che è già più pulito, e usi idrogeno da energie rinnovabili. Perché indico questi due Paesi: perché hanno tantissime aziende idroelettriche ad un costo di energia bassissima, 20 euro a MegaWatt. L’energia idroelettrica è quella che ha il rendimento più alto in assoluto. Allora tu sei in grado di usare l’idrogeno per il processo di immissione diretta, ma anche l’energia poi per il forno elettrico: questo cambia tutto il processo, arrivi a limitare le emissioni a 150 kg. di CO2 per tonnellata, contro i 2.500 kg. di CO2 per tonnellata di un altoforno: la differenza in termini di impatto ambientale è francamente enorme, parliamo di 20 volte meno.
Esiste un impianto così? Tu lo hai disegnato?
C’è a livello di prototipo, e vorrei realizzarne uno non appena possibile. È la mentalità che deve cambiare: mi serve tanta energia per un impianto? Bene, vado a realizzarlo dove posso averla a un costo accettabile. Penso ad esempio alla Grecia, dove c’è tantissimo vento, potrebbe essere un posto ideale dove hai sole, hai vento… Nel nostro settore, nessuno considera oggi la Grecia, eppure hai anche tante isole, e molte disabitate, vai a fare impianti li, così non ha neppure un impatto dal punto di vista della convivenza tra impianto e insediamenti umani. Poi c’è il tema dell’accumulo e distribuzione dell’energia prodotta, ed anche qui la tecnologia sta facendo grandi progressi.
Impianti del genere sarebbero redditizi già oggi?
Il profitto è legato a tanti fattori: la domanda, nel senso che un anno fa c’era una richiesta incredibile nel mondo e non c’era materia prima, quindi di conseguenza salivano i prezzi, ma anche i margini, e aumentava il profitto. Il profitto è generato poi anche dall’efficienza: se tu hai un impianto efficiente solitamente non fai errori. Poi c’è la manutenzione preventiva dei tuoi impianti, che non si devono mai fermare…Insomma, il profitto viene centrato quando sono in asse davvero molti fattori complessi. L’unica certezza che abbiamo, è che la scelta green non è alternativa al profitto, di questo siamo fortemente convinti.
Esistono fenomeni di green-washing anche nel vostro mondo?
Altrochè. Un cliente può dirmi: faccio l’impianto elettrico così sono a zero emissioni, e io chiedo “dove prendi l’energia per far funzionare l’impianto, dalla rete?”. Bene, da dove trae energia la rete? Magari dal carbone? Ok, allora l’intera filiera non è sostenibile, otterresti meno CO2 immessa se usassi i bruciatori a gas al post di prendere l’energia dalla rete. È come le batterie elettriche delle auto: è vero che l’auto elettrica non inquina, ma dobbiamo guardare all’intero ciclo di produzione includendo anche lo smaltimento, sennò facciamo puro greenwashing. Poi ovviamente la scienza e la tecnologia evolvono, quello che potrebbe non essere sostenibile oggi, potrebbe diventarlo domani.
Hai accennato al ruolo dello Stato come facilitatore di scelte più sostenibili.
Certamente. Noi in Europa abbiamo regole che in altre zone del mondo non ci sono, ad esempio altrove non c’è la Carbon Tax, eppure gli imprenditori dell’acciaio di quei paesi si stanno comunque spostando sul green, anzi, lo stanno facendo più veloci di noi. Perché? Per esempio in Giappone o in Korea hanno altri altiforni e hanno progetti consolidati che vanno verso la decarbonizzazione semplicemente perché diversamente il loro cliente non gli compra più l’acciaio. In definitiva, l’ultima parola è del cittadino, dell’utente, del cliente finale: la sensibilità cresce, e le persone si chiedono perché se è possibile inquinare di meno ciò non viene fatto? Quindi i gruppi dell’acciaio sentono la pressione e obtorto collo devono adeguarsi. Succederà entro un certo tempo quello che successo con le calorie sui cibi confezionati: quanta CO2 hai immesso in atmosfera per fare quella lattina di Coca Cola, questo è il messaggio, e quindi quanta CO2 hai immesso per produrre questa infrastruttura in acciaio? Chi arriverà primo su questo fronte, vincerà la sfida.
Ci sono realtà che spiccano particolarmente sul fronte del sostegno finanziario a questi progetti?
Il Giappone, ad esempio. Abbiamo adesso due progetti con clienti Giapponesi, dove stiamo approntando un processo di micro colaggio e laminazione continua senza forni di riscaldo. Ebbene, il governo ha compreso il valore del progetto e il loro Ministero dell’Industria, il MITI, ha finanziato il 100% del progetto ai nostri clienti, sostenendo a fondo perduto tutte le attrezzature e macchinari. Spettacolare sensibilità, che vorrei vedere anche in Europa. Praticamente in Giappone hanno un elenco di tecnologie, diciamo pre-qualificate, dove vi sono anche nostri prodotti: se il tuo progetto include queste tecnologie è finanziato in automatico, e la cosa notevole e che ogni hanno stanno aumentando i budget statali per questi investimenti, perché vedono che funziona.
Ultime battute: cosa diresti a te quaranta anni fa, e oggi a un giovane che iniziasse la tua carriera?
Di fare esperienze sul campo, perché si impara in un modo estremamente più rapido; e secondo di fare esperienze globali, stringersi il naso e andare ovunque, non dire solo “a me piace New York, Londra, Parigi”; no, io mi sono fatto andar bene l’isola di Sumatra dove mi sono trovato a quattro ore di distanza dal primo paese, piuttosto che nei sommergibili della Korea del Sud, e tutto questo mi ha permesso di contaminarmi con un insieme di culture, tecniche e stili di vita profondamente differenti, e di far mia quella curiosità intellettuale che mi porta a comprendere le persone prima ancora che parlino. Ho una solida formazione accademica, ma queste cose non le impari certamente in università, quindi benissimo l’università ma dopo devi girare il mondo, coraggiosamente, non accettando offerte solo nelle grandi capitali. Questo è il limite, ragazzi, muovetevi, fuori, fuori, fuori: fate esperienza, ma soprattutto vi fate conoscere, e tra l’altro crescete sia professionalmente che umanamente, e le due cose credetemi vanno di pari passo.
Il tuo più grande errore, e la cosa più bella che hai fatto…
Bilanciando ciò che ho detto prima, avrei vissuto di più, professionalmente, gli USA. Io sono rimasto stregato dalla cultura orientale e ho fatto moltissima esperienza ad est dell’Europa, ma dal punto di vista tecnologico non c’è niente da fare, le innovazioni vere si fanno in America, e se avessi fatto una parte più consistente della mia carriera in USA oggi guadagnerei 15 milioni all’anno. E per quanto riguarda invece le soddisfazioni, forse quando nel 2008 ho venduto la più grande acciaieria al mondo, a dei clienti giapponesi, a Tahara, vicino a Thoyoashi, clienti che non avevano mai comprato un chiodo da noi: quella è stata davvero una grande soddisfazione. Anche perché è difficilissimo vendere a loro, sono talmente meticolosi, seri e precisi… Ho vissuto anche qualche difficoltà interna, se così si può dire: a volte ho dovuto combattere contro una serie di corvi neri, tutti quelli che sperano che fallirai, che ti dicono “Ah, ci avevo già provato io…”. Poi invece se performi, se riesci, anche grazie a chi ti sponsorizza, che in questo caso è il mio Chairman che è un visionario, e ci ha creduto dal giorno uno, allora tutti, tutti, tutti, vogliono vendere quel prodotto lì, perché è l’unico al mondo, di fatto non c’è concorrenza qualificata e quindi diventa più facile venderlo.
Nella fattispecie, quale è il prodotto?
Questo nello specifico si chiama Q-ONE, è un forno elettrico digitale per la lavorazione dell’acciaio. È un prodotto moto complesso, sia dal punto di vista dell’hardware che del software di controllo, ma ci pone all’avanguardia nel mondo. Io comunque ci credo, e voglio ripeterlo con forza: l’acciaio verde è possibile, dobbiamo solo insistere convintamente in questa direzione. Le resistenze esistono, ma una volta intrapreso il percorso, non si tornerà mai più indietro.