Una “personal factory” in Calabria
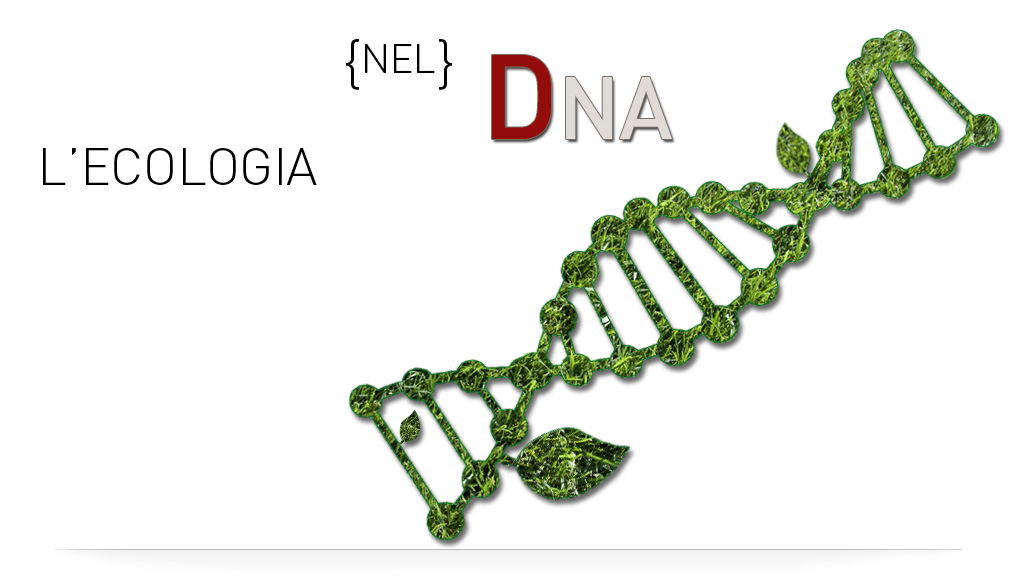
Cemento a chilometro zero?
Se le parole cemento e Calabria compaiono nella stessa frase di solito è per parlare di speculazione selvaggia. Dei chilometri di costa deturpati, di intere città fatte di case non finite che sembrano bombardate o di viadotti incompiuti, tristi ecomostri che allungano il loro collo di dinosauro sul nulla. Questa volta, invece, si parla di un calabrese che il cemento ha voluto reinventarlo fino al punto di smaterializzarne la produzione. Francesco Tassone, ingegnere trentenne di Simbario (Vibo Valentia), folti capelli ricci e tono di voce pacato, è convinto che il materiale più pesante da trasportare, più sporco e più old economy che esista possa diventare impalpabile, ecologico, in una parola intelligente.
“ Mio padre aveva un impianto di produzione di malte”, spiega Francesco. “ Sono prodotti per l’edilizia composti al 98 per cento da materiale inerte come la sabbia. Il restante due è chimica che aggiunge al materiale il colore o il grado di impermeabilizzazione. Gli impianti di produzione tradizionali sono grossi stabilimenti, con torri alte fino a cento metri che servono a miscelare i componenti”. Movimentare una merce così pesante ne fa crescere non solo il prezzo, ma soprattutto il costo in termini di inquinamento. “ Si calcola che il cemento sia responsabile del 6 per cento delle emissioni di CO2 di tutto il pianeta” chiosa Francesco.
La sfida di Francesco, fin dai tempi dell’università che ha fatto a Trento, è smantellare il vecchio modello per inventarne uno a chilometro zero. Perché non usare materie prime locali e non fornire solo la chimica? Perché non mettere in Rete l’esperienza e i bisogni di tutti gli utenti sparsi per il mondo? Nasce così a Simbario (30 chilometri dal Tirreno e 30 dallo Jonio, nel cuore verde delle Serre Calabresi) Personal Factory, una fabbrica smaterializzata in cui a viaggiare è solo il know how e non quintali di materiali inerti. Alla base del sistema c’è un brevetto, un macchinario chiamato Origami 4. Origami proprio perché è come se un grande stabilimento si ripiegasse su se stesso in appena sei metri quadrati. La mescola dei materiali inerti con la parte chimica (venduta da Personal Factory in apposite buste sigillate e dotate di un codice che ne identifica con precisione i componenti) avviene all’interno di un cilindro, mentre peso, quantità di materiali e tipo di malta da produrre sono regolati da un software. La macchina ha una capacità di sei metri cubi di materia prima ed è in grado di produrre e insaccare dagli 80 ai 100 quintali di prodotto finito senza essere ricaricata. Ogni ricarica richiede all’operatore all’incirca 10 minuti. Inoltre gli scarti sono quasi inesistenti e i tempi di pulizia sono inferiori a 10 minuti.
“Sono partito dall’idea del cloud computing per arrivare al cloud factoring”, spiega Francesco. “ Come nel cloud computing si offre un software comune che serve alle persone per lavorare insieme, così noi offriamo un software che permette alle nostre macchine di lavorare insieme. L’obiettivo è smaterializzare la produzione e distribuirla sul territorio mantenendo però la gestione dei dati in un cervellone centralizzato. È come avere una stampante a centinaia di chilometri dal mio computer”.
A oggi sono state installate macchine in Tunisia, Calabria, Sicilia, Puglia, Abruzzo, Toscana,Lombardia e, a breve, anche in Campania e Lazio. E ogni microbetoniera è monitorata dal software collegato via Internet al centro di controllo di Simbario. Ogni busta di componente chimica (il know-how “fisico” che Personal Factory vende ai clienti), grazie al suo codice che la macchina è in grado di riconoscere, è la “chiave” che permette alla Origami 4 di procedere con la mescola e l’insaccamento delle malte. “ Nell’era di Internet non è più necessario spostare merci. Basta spostare le informazioni”, conclude Francesco. “ Non servono più le grandi fabbriche ma strumenti flessibili, connessi e intelligenti da dare agli uomini: strumenti programmabili in base al contesto in cui si trovano”. Se la Origami 4 è il braccio, una specie di microbetoniera evoluta, il sistema centralizzato di cloud manufacturing è il cervello. Della squadra fanno parte anche il babbo Giuseppe Tassone, 66 anni, e Luigi, il fratello venticinquenne di Francesco, ma chi ha in mente la solita aziendina familiare è fuori strada. Questa è piuttosto l’avanguardia di una rivoluzione possibile. Quella che il blogger inglese Cory Doctorow ha battezzato la subcultura dei “makers”, cittadini comuni capaci, grazie all’innovazione tecnologica e all’hacking di hardware e di modelli di business, di togliere all’industria manifatturiera il monopolio della produzione in serie. Personal Factory però è anche la storia di ragazzi calabresi che potrebbero lavorare benissimo altrove, ma hanno scelto di non arrendersi e non andare via.
“Questa è casa mia”, sottolinea Francesco Tassone. “ Ma non sopporto il fatalismo di qui: l’idea che siccome non c’è niente, allora non potrà mai esserci niente”. In un territorio dove l’unica economia è quella dell’assistenzialismo (il Comune con i suoi 50 dipendenti è il principale datore di lavoro) Personal Factory potrebbe presto diventare il nuovo motore di sviluppo della zona, ma la strada è tutt’altro che in discesa. “ Oggi finalmente è arrivata l’Adsl in tutto il paese”, spiega Francesco, “ ma solamente perché il ministero degli Interni ha cablato tutte le caserme dei Carabinieri. C’è una sola ragione che mi spinge a rimanere qui: voglio trasformare questo paesino di montagna in un posto in cui una nuova generazione di innovatori possa essere in grado di fare impresa e produrre tecnologia. Spero che guardando a quello che stiamo realizzando qualche giovane calabrese diventi più audace e invece di pensare che “tanto non cambia mai niente” possa convincersi che sì, “‘si può fare’”.